压力传感器的蠕变(Creep)是指在其承受恒定载荷时,输出信号随时间发生缓慢漂移的现象。这种现象主要由材料特性和压力传感器设计中的多种因素引起,以下是具体原因及机制:
1. 材料本身的蠕变特性
弹性体材料的粘弹性:
传感器的弹性体(如铝合金、不锈钢或合金钢)在长期受力时会发生粘弹性变形。即使载荷恒定,材料内部的分子链会逐渐重新排列,导致微小但持续的变形。
高温环境会显著加速这一过程(例如金属材料的蠕变在高温下更明显)。
聚合物材料(如胶粘剂或弹性体填充物)的蠕变效应更为显著。
应变片基底材料的蠕变:
应变片的基底(如聚酰亚胺)或胶粘剂在受力时可能发生缓慢变形,导致应变片电阻值漂移。
2. 结构设计与应力分布
局部应力集中:
如果弹性体设计不合理(如过渡圆角过小或截面突变),某些区域可能因应力集中而加速蠕变。
残余应力释放:
制造过程中的机械加工、热处理或焊接可能引入残余应力。长期受力时,这些残余应力逐渐释放,导致输出信号漂移。
3. 环境因素
温度波动:
温度变化会导致材料热膨胀系数差异,引起附加应变。即使载荷恒定,温度变化可能被误判为蠕变(需与真实蠕变区分)。
湿度影响:
某些材料(如胶粘剂或复合材料)吸湿后发生膨胀,导致应变片基底变形。
4. 胶粘剂与安装工艺
胶粘剂蠕变:
应变片通过胶粘剂(如环氧树脂)固定在弹性体上。胶粘剂在长期剪切应力下可能发生蠕变,导致应变片与弹性体之间产生微滑移。
固化不充分:
胶粘剂固化不完全时,内部分子链未充分交联,长期受力后逐渐变形。
5. 蠕变与恢复特性
蠕变恢复:
卸载后,压拉力传感器的输出可能无法完全归零,称为蠕变恢复滞后。这是由于材料变形未完全弹性恢复,存在塑性变形或分子链重排的延迟效应。
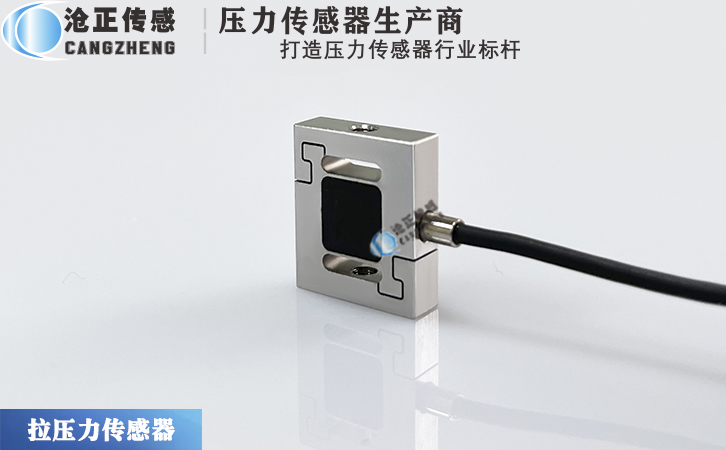
如何减少蠕变的影响?
材料选择:
使用低蠕变材料(如铍青铜、特种不锈钢或陶瓷)。
选择高稳定性的胶粘剂(如酚醛树脂或高温固化环氧)。
优化结构设计:
避免应力集中,采用均匀的应力分布设计(如双剪切梁或全桥结构)。
增加弹性体刚度以提高抗蠕变能力。
工艺控制:
确保胶粘剂充分固化,减少残余应力(如通过退火处理)。
采用激光焊接或一体化加工减少装配应力。
温度补偿:
加入温度传感器,通过算法补偿热漂移。
选用温度系数匹配的材料(如弹性体与应变片基底的热膨胀系数接近)。
预加载处理:
对压力传感器进行预加载老化,使其在出厂前完成部分蠕变过程,提高长期稳定性。
示例分析
金属材料传感器:不锈钢传感器在常温下蠕变较小,但在高温(>300°C)或长期重载(如起重机称重)时仍可能发生明显蠕变。
低成本传感器:使用铝合金和普通环氧胶的传感器,在潮湿环境中易因胶粘剂吸湿导致蠕变误差。
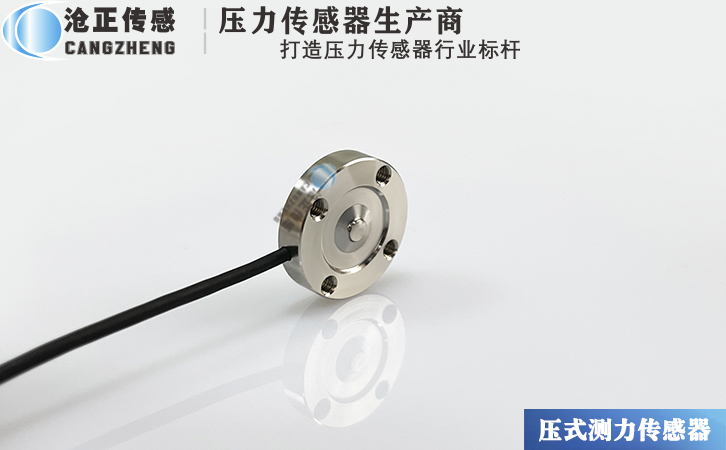
压力传感器的蠕变本质上是材料在时间和应力作用下的非弹性响应,需通过材料、设计和工艺的综合优化来抑制。在需要高精度长期测量的场景(如航空航天或精密称重),需选择经过严格蠕变测试和补偿的传感器。